600 employees reskilled in just a few months
93% of companies view adopting new technology, like robotic material handling, to improve team performance as important to their organization’s success. Even factoring in maintenance costs, depreciation, and time to profitability, the cost makes sense when a company forecasts a significant increase in production. But without the proper support for employees using the tools, these types of investments often fall short of expectations and can even fail.
To be successful, many companies are realizing the need to retrain their existing workforces. With the right tools, you can provide your team with the support they need to master new skills faster and reduce their time to proficiency. Reskilling or upskilling are a necessary means for companies to improve team capabilities alongside the rapid digitalization of the workplace.
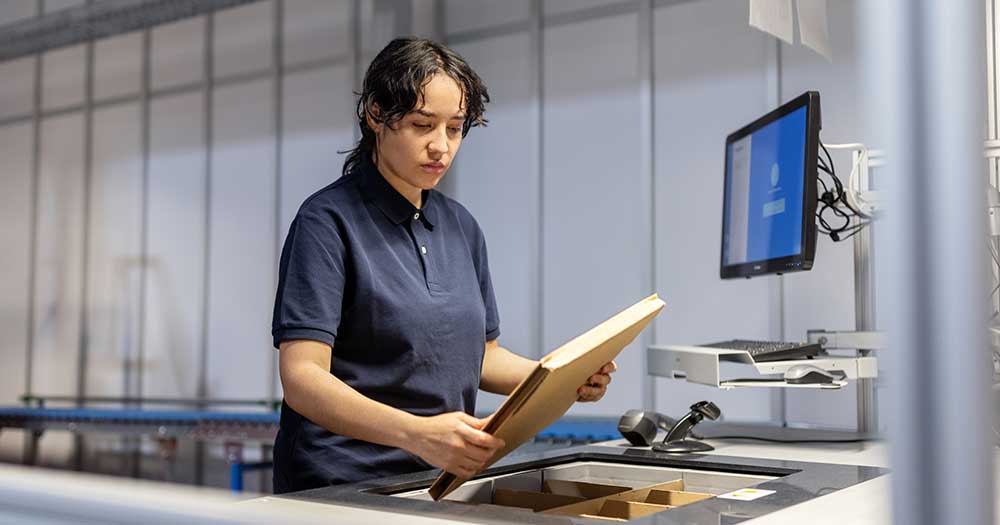
Outcomes:
- 600 employees reskilled in just a few months
- Increased efficiency to double the number of pallets packed/hour
- Rapid adoption of new technology with virtually no downtime
- Reduced travel waste & Improved pick rate
“Thanks to Acadia, employees view the role changes as personally beneficial – an opportunity to simplify work and learn new skills.”
– Operational Excellence Manager
One of our clients is an aftermarket automotive parts manufacturer and distributor. They’ve recently been undergoing a major transformation to improve how they fill customer orders.
The transformation comes at a time when they’re experiencing growing demand and a shrinking workforce as many tenured employees retire.
In their distribution facilities, “travel waste,” the time it takes an employee to travel from one picking location to another, was the main inefficiency. One employee picked the entirety of an order. No matter where the product was located in the 750,000 square foot warehouse, employees would walk aisle to aisle to retrieve and add it to the order.
To increase efficiency, the company localized pickers to part-specific zones and invested in autonomous mobile robots (AMRs). These transport robots independently move products from the picking zones through the warehouse to a centralized packing location, eliminating unproductive travel time.
In addition to the robots, Vertical Lift Modules (VLMs) were installed to further consolidate picking and packing zones and improve how customer orders are filled. These fully automated vertical storage systems take up less floorspace and allow them to condense 30% of all picks, 11,000 SKUs, and eliminate 138 feet per pick.
Introducing such a transformational change in the way the facility operated meant that everyone on the team immediately had a skills gap. 250 employees’ jobs changed entirely. Others needed to be trained to maintain and troubleshoot the AMR fleet. And some needed to be cross trained to operate the VLMs as well. In total, 600 employees had to be re-trained to do parts or all of their job.
“Automation” can be a scary word for many people. So, another concern for management was to help employees feel comfortable and confident with the changes.
Acadia helped them simplify complex procedures, close the skills gaps, and do it in a way that employees didn’t become overwhelmed.
They created comprehensive SOP documents employees use for training, revisit on the job, and reference an average of 4 times a day. With Acadia, they created an AMR manual with acknowledgments, quizzes, and procedures and incorporated it into their leadership training regimen.
By using Acadia SOPs to train employees, AMR onboarding and use became the most successful project in years. The operational excellence manager said Acadia has decreased employee apprehension and made automation and new technology more exciting. The changes were adopted with minimal disruption. No orders were delayed and it’s even led to promotions.
“Employees now think, with the help of Acadia, the changes have been personally beneficial, an opportunity to simplify work and learn new skills.”
Ready to crush your goals?
"*" indicates required fields