Exceeding Gross Line Yield Targets within 6 Months at Each Plant
One Best Way work procedures – in the form of SOPs or other work instructions – help team members perform their tasks the right way, every time. When SOPs aren’t easily accessible and team members aren’t held accountable to them, mistakes are made causing rework and even injuries. Operating costs impair profitability, and customer service and product quality become less reliable.
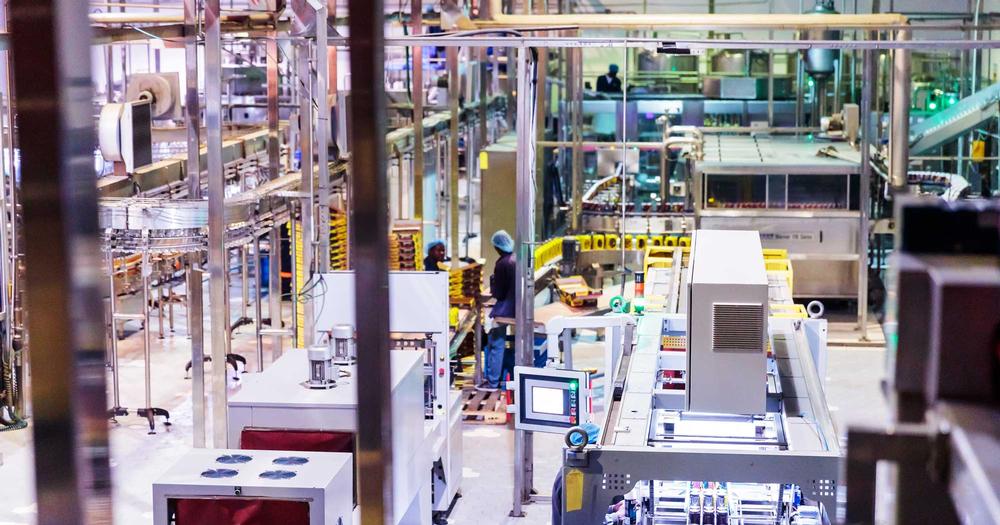
Outcomes
- All Acadia-enabled plants, running the system 6 months or longer, exceeded their gross line yield target.
- Quality has increased as measured by pre-established Quality KPIs.
- Safety has improved as measured by injury reduction.
- SOP Compliance correlated directly to performance. When SOP compliance met expectations, line efficiency was also at its highest.
“The SOP transition to Acadia is one of the most important initiatives we have done in the last five years.”
– North American Director of Operations
New Capabilities
- Visibility and accountability drive SOP compliance
- Best practices tied to KPIs shared globally
- Team member behavior change directly correlates with KPI values
- Team member engagement promotes continuous process improvement
At the enterprise level, when each location adopts its own processes and systems for managing SOPs, efficiencies are harder to identify and nearly impossible to share from location to location.
Prior to deploying Acadia, our client had separate systems for creating, managing and tracking SOPs at each of its global facilities. In many cases, the SOPs were deployed on paper, making it difficult to track adoption and compliance.
Now, as nearly all facilities have converted to Acadia, paper is being eliminated and replaced with a robust digital platform. It provides job aids to team members as they complete their daily tasks and enables them to provide feedback on process improvements. It also helps managers see which team members are following One Best Way procedures and which ones need more training support.
At full deployment, the client will see advantages beyond the line efficiency improvements at individual locations. They will be able to share best practices across all locations, making their global continuous program even more powerful.
Ready to crush your goals?
"*" indicates required fields