Remove Cost & Waste While Building Employee Confidence
Safety, quality, and efficiency depend on your ability to provide actionable information to teams.
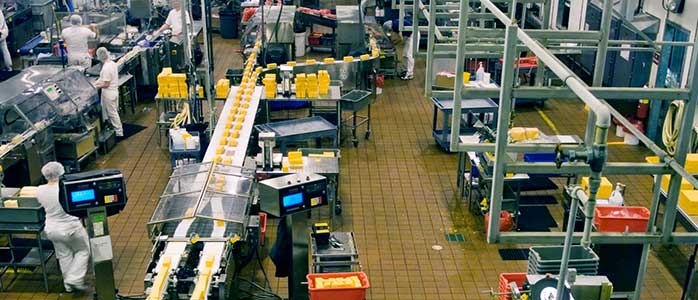
If your teams are slowed down because best practices are all in the heads of your group leaders, if training is done shoulder-to-shoulder, and quality control isn’t audited, you’re missing critical opportunities to cut cost and waste from your operations.
Acadia enables you to:
- Capture process knowledge from retiring team members
- Provide standardized onboarding & training that is less labor intensive
- Deploy dynamic SOPs, work instructions, and job aids for manufacturing, quality, and maintenance teams
- Communicate critical safety information efficiently to all team members
Single Source of Truth
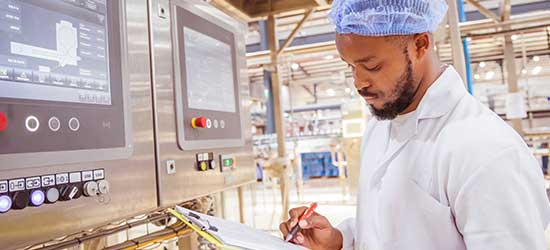
Delivering critical information can be obstructed by a lack of documentation or deploying work instructions and training through labor-intensive, shoulder-to-shoulder instruction. This can create safety, quality, and efficiency challenges that are limit a plant’s production capabilities.
By deploying dynamic SOPs, active work instructions, hands-on training tools, and on-demand job aids to your operations teams, you can eliminate confusion and firefighting when things go wrong. It will also prepare you for disruption that comes when team members retire over the next several years.
SOP Compliance = Process Improvement
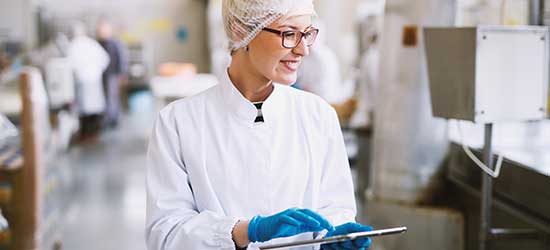
Plant SOP compliance correlates to improvements in critical quality, efficiency, and yield targets at an Acadia client operating globally:
- All Acadia-enabled plants, running the system 6 months or longer, exceeded their gross line yield target last year
- Quality has increased as measured by pre-established Quality KPIs
- Safety has improved as measured by injury reduction
- SOP Compliance correlated directly to performance. When SOP compliance met expectations, line efficiency was also at its highest
- Engagement scores of Acadia are over 90%
The SOP transition to Acadia is one of the most important initiatives we have done in the last five years.
– North American Director of Operations
Training & Onboarding
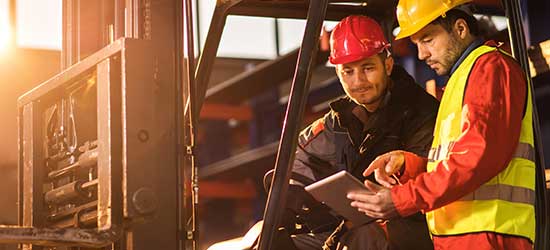
Consistent process outcomes start with your training approach. We learn better while doing, so job-embedded training programs are immediately more relevant than classroom or course-based activities. They take less time. They require less effort to pay attention. Most importantly, they stick.
Acadia improves training effectiveness by injecting training directly into work. Employees have easy access to SOPs and other job aids at the moment they are performing the task. Managers can check comprehension with quizzing and evaluations to ensure everyone gets the support they need.
By making training more efficient and productive, new employees get up to speed more quickly and they gain the confidence they need to stay.
More on training:
- Retention starts on Day 1
- Process training that helps your team learn faster
- Cementing process knowledge in place
Audit Trail & Accountability
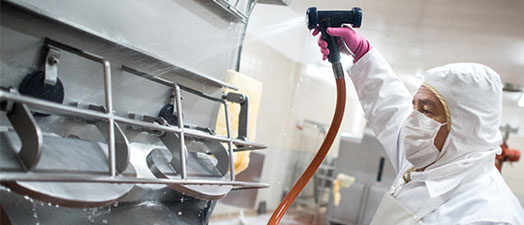
In most operations, SOP compliance correlates directly to performance. When compliance expectations are met, rework, yield, waste, and safety KPIs are also improved.
Managers with visibility into employee SOP compliance can identify who is performing tasks the right way and who might need additional training or support. By digitally tracking compliance, you also create an audit trail that can help you comply with ISO standards, OSHA regulations, or FDA guidelines.
If your visibility into compliance is limited because maintenance protocols, quality procedures, etc. aren’t documented, you’ll find it more challenging to extract benefits from process improvements.
Making accountability part of workflow:
Safety Protocols Deployed in Minutes
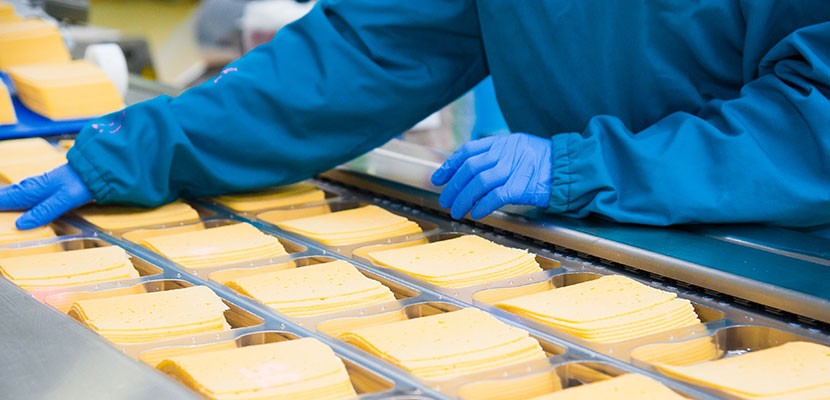
Updates to safety processes at an Acadia client are updated and relayed to employees globally in 15 minutes
- Safety protocols sent to all facilities could not be tracked. Now safety team knows when protocols are received and read by each person
- Policies and procedures from binders, spreadsheets and various software programs consolidated into a single source of truth
- Manual audit process that previously took a team of managers three months to complete is now done in about a month
- Next steps, layered process audits in manufacturing
Acadia gave me two months of my life back. The manual work I was doing on site has been eliminated. Now I can spend my time walking the floor.
– Dir. Corporate Safety
Employee Engagement
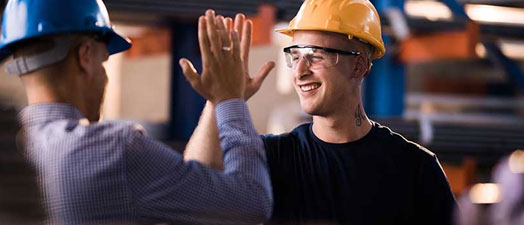
Bottom-up improvement is effective because frontline employees are closest to the problems and are best able to identify and solve them.
When your employees are empowered to improve their work processes, they will make their tasks as frictionless and efficient as possible. When they feel ownership of their process, it is easier to hold them accountable to it. When these things happen naturally and continuous improvement has become part of your culture, your employees will feel more ownership in their work and become less likely to leave.
Retiring Workforce – a real-world example

Progressive operations teams are using technology to retain organizational memory from outgoing team members and pass it to those who replace them. When done correctly, this can have minimal impact to production.
Recently, one of our clients was working to fill an internal skills gap by developing a 17-week program to identify future managers. The program trained applicants on multiple roles for their manufacturing facilities. Instead of relying on presentations in a classroom setting or printed instructions, each employee was given access to Acadia on a mobile device.
- Procedures required to perform each role were easy to find and could be retrieved as the person performed the work.
- Procedures were automatically transformed into a series of step-by-step task lists.
- Each task was simple and clear, and many had accompanying job aids such as diagrams or videos that helped provide context and further instruction.
- Employees could also provide feedback, as they worked, when instructions weren’t clear. This helped the instructors to improve procedures for the next group of trainees.
Because the task lists were completely auditable, the instructors could see which employees were using the procedures most effectively and which needed additional support. Trainees were also quizzed regularly to help identify those who should spend more time on a particular procedure and those who could advance.
With the success of the reskilling program, the company began to close its workforce gaps. It also expanded the use of Acadia to all line workers. Since launching the broader program, the company has begun closing performance and training gaps, exceeding gross line yield targets, meeting quality KPIs and reducing injuries.
Enterprise Ready, but without the headaches
Acadia is workplace tested and built to serve the needs of large organizations first. Our standards meet the most rigorous requirements of our enterprise customers working globally in manufacturing and other highly regulated industries.
"*" indicates required fields
Ready to crush your goals?
"*" indicates required fields