Paper SOPs Kill Your Efficiency
On-demand information for team members builds confidence, and makes team members more productive.
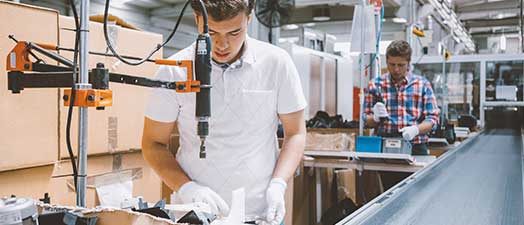
We work with manufacturers to help them:
- Quickly onboard and train new hires without distracting top performers
- Upskill existing team members while they work in new positions
- Make it easy for everyone to follow One Best Way procedures
- Target operator issues related to waste, productivity, and safety
All of this is possible when you deliver work instructions and job aids to your teams on the line, validate their comprehension, and capture their feedback.
Well-trained team members are more confident and stick around
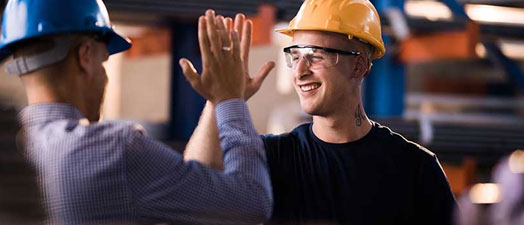
Everyone is struggling to find skilled workers for specialized roles and most are having trouble hiring even entry-level positions. Retention and upskilling have become an urgent priority for most companies.
Bolster confidence by making knowledge tools easily available:
- Single source of truth work instructions and job aids
- Hands on micro-learning for new processes
- Feedback that helps them improve and advance
You’ll hire and onboard faster, make teams more productive, and keep the people you have.
Rapid Continuous Improvement
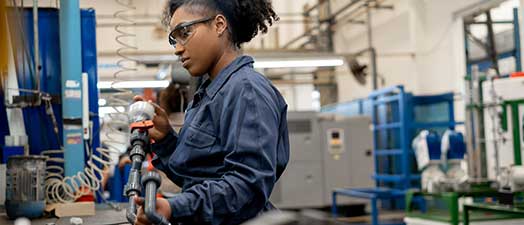
Track SOP compliance by integrating critical tasks with waste and downtime metrics to understand where your processes can be improved.
Provide your teams with the information they need to do their work correctly and they’ll make fewer mistakes. They’ll spend less time figuring out how to do things the right way. Instead, they’ll start offering suggestions for improvement.
When you integrate your team’s activity on Acadia with your production data sources. You’ll quickly see how SOP compliance for critical processes relates directly to your waste and productivity KPIs.
Rely on employees for their ideas and insights
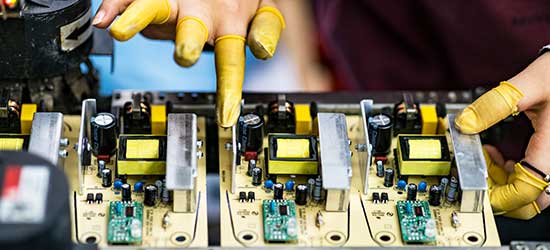
Capturing feedback from your team while they’re working on tasks can yield significant process improvement ideas.
One of our manufacturing clients had a machine with a worn part that was creating unplanned downtime. The problem was, nobody really knew about it, except for the line employees working at the machine. There wasn’t a clear method to escalate the issue, so they just cleared the machine and went on with their work.
The same day the employees gained access to Acadia, they shared photos of the damaged machine back to the plant manager. He quickly worked out a solution and fixed the problem permanently.
It’s unclear when or if the manager would have learned about the issue without this feedback, but the amount of waste saved by the fix is adding up quickly.
We have dozens of similar stories of process improvements, waste reductions and new efficiencies that have come from our clients’ employees.
How can we help?
With Acadia, you can easily and inexpensively manage standard policies and procedures, track compliance, accelerate learning, and achieve behavior change.
"*" indicates required fields
Ready to crush your goals?
"*" indicates required fields