Business Process Activation
Close the gap between process definition and execution.
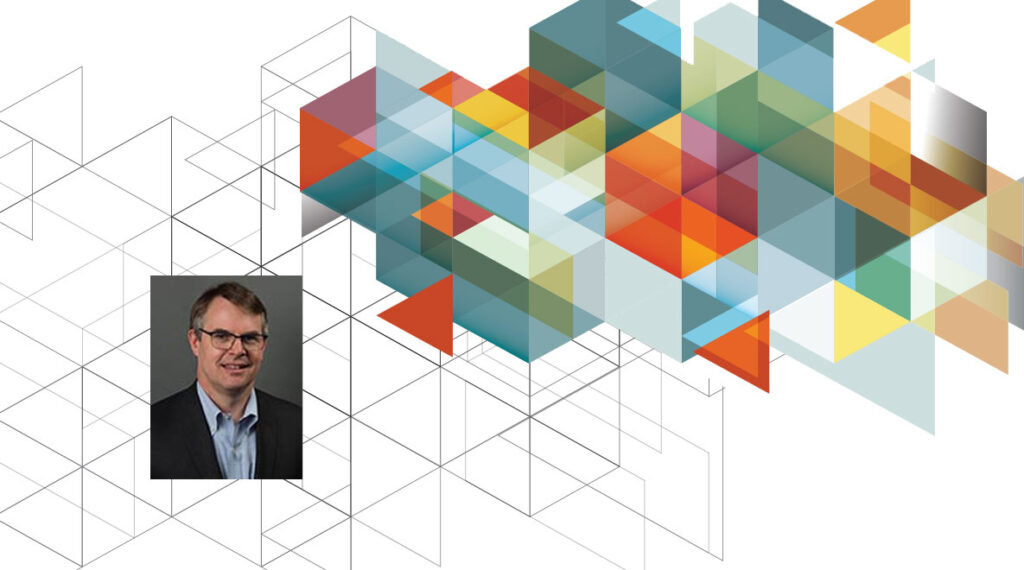
Companies invest significant effort designing and developing corporate business systems and defining best business practices. While the work of process leadership teams and anointed “process owners” is often well thought out, moving from ideas to actions and results is difficult and can be frustrating to leadership and to those leading the charge.
While executive vision and leadership is needed to start a transformation, gaining user-level buy in and building a culture around standard processes and best practices requires patience and focus. Simple tasks, like capturing user feedback and updating and maintaining standard operating procedures (SOPs), can be time consuming and complex. Having led corporate business system and process-driven transformations, I am always looking for leading ideas and tools to enable their success. I recently came across an interesting solution set from Acadia, which closes these gaps and more.
The missing link(s)
While no one can disagree that having a best practice or SOP shared across an organization can be powerful, the typical tools in place at most organizations do not support a truly effective process deployment. How are recommended changes captured? What is the latest version? Who is the owner of the process? This is only the tip of the iceberg.
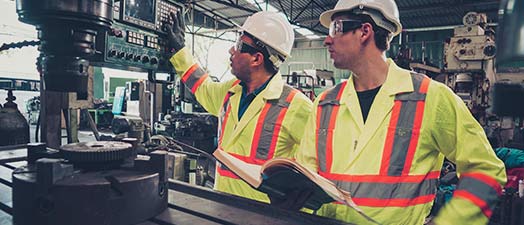
How about gaining real time feedback, consolidating performance data, and confirming acknowledgement of changes? With the right person leading a specific effort, this can be accomplished through brute force, but small changes in an organization’s leadership can disrupt progress.
Driving sustainable change – a safety example
In order to drive sustainable change, core processes and best practices need to be visible and maintained on a real-time basis. This can start small but will drive significant impact without needing top-down mandates. What are the top ten safety learnings’ best practices across a distribution network? Have they been reviewed by the local leadership team? How do regional regulations vary across your locations? Have the team leaders been trained on what to look for to avoid repeat incidents?
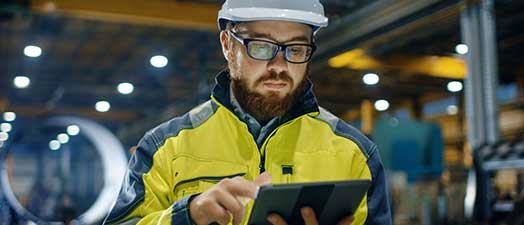
Building a safety culture often involves more listening than telling. It is difficult to listen when an organization is spread across regions and organizations. The result is usually a surge of action following an incident that can quickly wane.
One of Acadia’s customers is a consumer durable manufacturer with a safety team of 2,000 operating in plants around the globe. The safety team invested heavily in safety protocols, but hadn’t invested in a system to manage, distribute, and report on their adoption.
With a framework cobbled together from a traditional document management platform, spreadsheets, and printed documents, managing the system required excessive people hours. The safety leadership team, for example, would spend three months per year auditing each manufacturing facility in person.
After converting to Acadia, the safety team has eliminated two months of manual work from their annual review process. Updates to policies in response to an incident can be distributed across the enterprise immediately, instead of after several hours or days. Reporting shows when each employee has viewed and acknowledged the new protocol, instead of waiting for the annual audit. The end result is a more engaged team and most importantly a significant reduction in safety incidents.
Overcoming the challenges
Having participated in and led corporate business system development and having led large functional teams, I have seen the challenge of keeping processes “evergreen” and activating the benefits of best practice and key learnings. What I know is that the power of knowledge, experience, and ultimate action sitting in plants, DCs, and remote offices is what is needed to effectively drive and sustain results.
Shoulder-to-shoulder and classroom training is inefficient and with staff shortages, it takes time away from the team members who we can’t afford to lose. Self-guided training while performing work activities is a more efficient method for making best practices stick. It’s also a more pragmatic way to reskill teams to adopt new technologies.
Imagine providing a team with immediate access to best practice work instructions, and other job aids, while they perform a task. Now empower that team to provide feedback on the process as they work. The gain in efficiency from everyone following the same playbook is multiplied when the process is continuously improved by the folks doing the work.
Getting started
The beauty of Acadia is that things can start small and build. What is the one process that needs to be shared? What team expends the most effort managing processes? Focus on that one to develop and build an approach to fully activate the objectives of the team. Then find the next team and the next project.
In fact, every enterprise company working with Acadia has started with a single, actionable use case. The Acadia team helps to scope the project and identify KPIs that can be used to gauge progress. As a realistic workflow is established within the organization, the pattern can be repeated. In addition, robust analytics on user interactions helps to guide priorities and enables process continuous improvement.
At a large beverage company, their trial project was a training initiative for new plant managers entering the business. Over the course of 17 weeks, a cohort of new managers were trained for multiple line roles using hands-on instructions in Acadia. After the successful pilot project, the company tried Acadia in a variety of other locations, including corporate back office functions before implementing it across global manufacturing operations.
Global best practices and SOPs are powerful and only get better with active and ongoing development. That said, the best processes you can build are worthless if they aren’t being used.
About the Author
Steve Vielmetti is a senior supply chain executive with an extensive range of experience across automotive, industrial, consumer product, and apparel industries. He has led end-to-end business system deployment, network and inventory optimization, mergers, divestitures, and other business transformation projects. He has deep knowledge of critical IT systems and supporting processes including ERP, supply chain planning, transportation and warehouse management, optimization and analytics.
Ready to crush your goals?
"*" indicates required fields