Continuous Deployment – Immediate Benefits – Sustainable Change
How to focus less on the process and more on the results
- Simple approaches can fast-track progress on even the most complex projects.
- Incremental changes make the larger goal more attainable.
- Don’t let a large goal lose momentum because of its scope. The important thing is to get started.
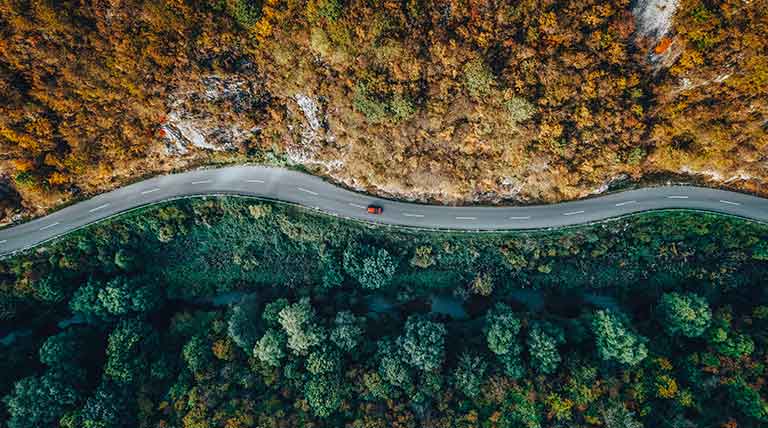
Call it what you will — continuous improvement, lean, six sigma, kaizen — companies in every industry are finding success by making incremental, ongoing improvements to processes, products and services.
While the process may be incremental, the results are anything but.
- Healthcare providers see dramatic increases in the quality of patient care and decreases in staff turnover by implementing seemingly small measures.1
- Manufacturers find a competitive edge through cost savings, product improvements and risk reductions by sharing ideas across all of their locations.2
- Service providers keep customers happy and bring in new ones through superior customer service that spans online, phone and storefront operations.3
All too often, we see clients who are eager to adopt a culture of continuous improvement in their business, stall out before they get started.
Changing the culture of your company is no small task. As you begin to think about all the different departments, people and resources needed to pull it off, it can feel overwhelming. Sometimes frustration with the distance to the goal can discourage us from getting started.
What we’ve found works best is to make the process of adoption and deployment continuous as well.
Incrementally deploying processes
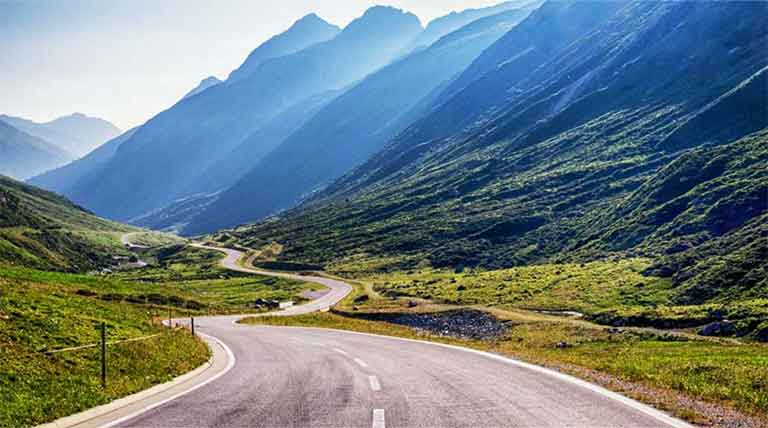
If your policies, procedures and other job aids are perfectly documented and you have a process for editing them and updating them already in place, that’s great! That puts you ahead of the curve. If you’re not quite there yet, you may find it’s more productive to start developing those documents within a system, rather than trying to plan it all out in advance.
One of our government healthcare customers is responsible for managing, processing and regulating the operating licenses for care provider facilities statewide. For each of the 33 types of facilities the office oversees, there is a different set of standards and requirements that need to be met. This means that each of the office’s staff members needs to be trained on the requirements for the facilities they will regulate, as well as the back-office procedures they need to follow when filing reports.
Initially, our customers were working from a series of hundreds of PowerPoint documents that were managed on a local server. It was difficult to control versioning, editing and updating. It was also challenging to find the right document at the right time to perform tasks.
The office’s executive director chose Acadia to manage policies, procedures and manuals, as well as create check lists and track progress for new employee onboarding. There was a lot of information to capture and enter into the system, but the director thought of an ingenious way to get the project going.
She asked everyone on her team to identify the processes they felt were most important to their daily work and enter that into Acadia. This accomplished several things at once:
- She learned what was most important to each of her team members.
- Critical information that, up until then, was only in the heads of employees was now captured.
- The team became familiar with the platform and began to think of better ways to enter information.
- Best practices that were identified could be immediately shared across the team.
- Everyone was engaged in the process and could provide feedback, making buy-in a non-issue.
With this simple approach, the office was able to fast-track a process that otherwise may have taken months or not even happened at all.
Incrementally deploying across business units
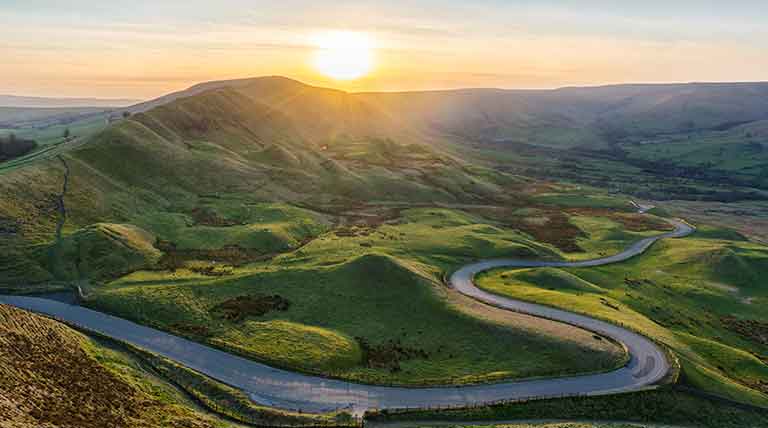
The healthcare quality office example works well when a single team controls all of the processes and documentation used by the department, but what happens when the organization has national or global dimensions?
About a year ago, we started working with a large global brewing company. Their interest in Acadia was to replace a paper-based SOP system that was cumbersome and hard to track. They knew modernizing their system would not only help make individual plants more efficient, but they also expected to unearth best practices that could be shared among all their facilities.
Rather than try to sort out how to implement the new platform across all global properties at once, the company opted for a pilot program that would help them understand how it worked and how it could be used.
They landed on their brewery training program. This was a 17-week, hands-on program that allowed new employees to rotate through several different roles in the brewery. Because the training program was new, it was easy to adopt a new platform and see if it performed better than their existing Learning Management System (LMS) and paper-based SOPs.
SOPs were available on mobile devices and could be converted to task lists, so the trainees could be trained with and then use the same documents in real world scenarios. This was particularly helpful in the short period of time the trainees had to learn procedures across multiple roles.
The program was very successful and the project manager in charge of it received a lot of positive feedback. More importantly, trainees learned faster and retained more of what they learned.
The company decided it was time to expand their pilot to an entire plant.
After adding documents into Acadia and training staff, the brewery worked out bugs, found better ways of doing things and eventually completely replaced their former system.
Again, the company could see positive results as the plant using Acadia closed performance gaps and increased employee task proficiency. With each success, the company expanded adoption to additional locations. Today all North America breweries and bottling plants have switched to Acadia or are preparing to convert over.
The takeaway for us in these, and many other scenarios we’ve encountered, is that it’s easy to get hung up on the implementation process. But that loses sight of the purpose of continuous improvement. Whether you start small or start big, you will learn and improve just by starting.
Sources:
Ready to crush your goals?
"*" indicates required fields