3 Keys to Survive Today and Emerge Tomorrow as a Stronger, Safer Business
Agile businesses that leverage the right technology, processes, and talent will position themselves for future success.
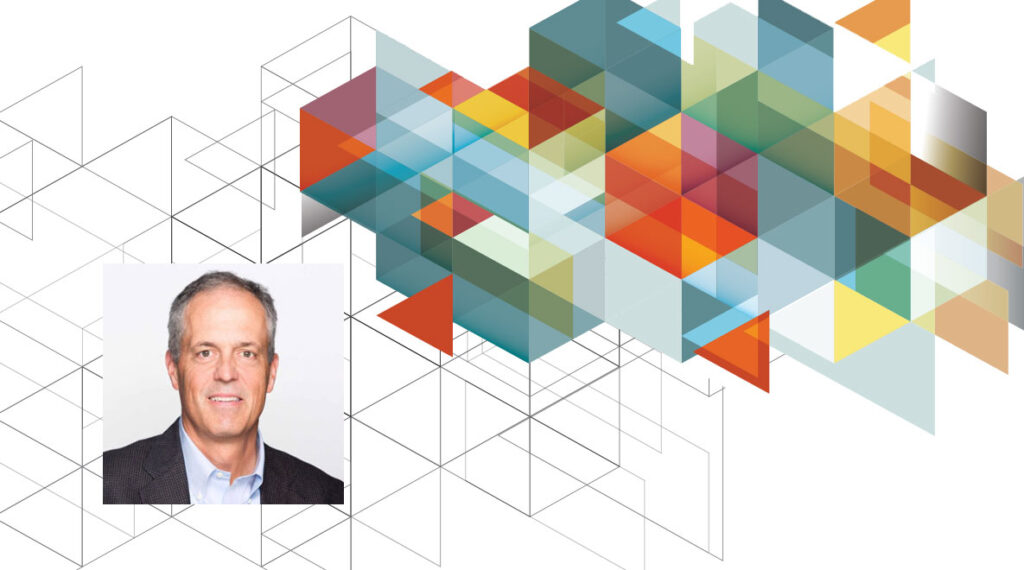
Prior to 2020, the rationale for implementing business process tools and new technology was largely based on cost competitiveness, customer service improvements, and incremental revenue growth. Now, and for the foreseeable future, health and safety will influence the competitive equation in ways it never has before.
Businesses have long recognized the importance of health and safety in their operations, particularly relating to hazardous work. Addressing these concerns has become increasingly complex as nearly every work environment is now potentially hazardous as a result of the global pandemic. The health and safety of employees, customers, and partners in day-to-day operations has suddenly become a strategic priority for all businesses across all levels of operation.
The following are three keys for surviving today and emerging stronger tomorrow, with greater health and safety in place: One Best Way Processes, Edge Sensing Devices & Networks, and Augmented Planning Insights. These tools are now a strategic necessity for business survival.
The good news is that the tools are already available, vetted, and validated in compliance industries such as healthcare and the food cold chain. Businesses that have reacted to the current crisis by relying heavily on the above-mentioned capabilities have experienced much success. Companies that have not yet focused on incorporation of such tools, as part of their digitization strategy, should consider them now to proactively move to an improved safety footing.
Regardless of your level of adoption of these resources and whatever your technological capabilities may be, any increase of visibility into your operations has value. In situations involving people, the more visible you can make your operation, the safer everyone will be.
1. One Best Way Processes
The tip of the spear for keeping people safe in their working environment is the ability to establish, communicate, enforce, and continuously improve One Best Way processes. This is a fertile area in business today in light of the current pandemic and industrial accidents in the recent past. It should take no more than 15 focused minutes to refine and push out new policies and procedures to all employees. Once communicated, the policies and procedures should be reinforced with new governance models to ensure compliance, with visibility across the globe.
Companies that have mastered this safety monitoring capability, by deploying systems like Acadia, understand and can track the following with precision:
- who has received a new process
- who is impacted
- who is compliant in following it
- who needs more training
- what non-compliant situations need to be addressed urgently
Business leaders who utilize this data and continuously seek feedback from employees can refine processes and improve performance over time.
We should consider the current pandemic scenario facing employers across every industry as the “Manhattan Project of Going Back to Work” and view it is as a global economic and employee safety priority. The reality is that whether your employees work in the back office or on a factory line, they need to completely change their behaviors to protect themselves and the company’s customers from infection. This is the “next new normal” all businesses must acknowledge in their operating models. It not only addresses the current pandemic response but prepares companies for the next inevitable disruption. New procedures for social distancing and sanitation best practices, track & trace, sensing, enforcement, and analyses must be embedded in the business operating model.
Without an enterprise-wide performance management tool ensuring One Best Way employee safety processes, a business may have to rely on printing policies and procedures on paper, distributing them via email, or directing people to search share drives. However, these methods only allow for static and dated views of compliance and performance. None give you the real-time reassurance and status that the processes have been read, put into action, and tracked.
Here is an example of success. Over the last month, one of Acadia’s global CPG clients developed and then immediately distributed new work protocols across North American operations. Each employee was required to review and acknowledge the procedures before returning to their day to day line assignments. Managers could immediately identify who had seen and read the directives and who had not. They were able to reinforce training with the employees who hadn’t seen them or were not acknowledging them. The ability to sense and respond to safety procedures across the business instantly is a significant opportunity for companies to prioritize. There is massive risk if these procedures and compliance are not tracked and managed by the business leaders in real time. This is especially true for people working in hazardous areas.
In addition to sending new policies to employees for acknowledgement, the aforementioned Acadia global CPG client integrated the new information directly into work instructions used by their employees day-to-day. These instructions were broken into a series of task lists so that the component activities could be tracked, traced and enforced on a continuous basis. Any additional, new tasks in the workflow could be easily introduced, deployed and adopted. From a compliance perspective, employees were required to check off each task upon completion so that the business has an auditable record when new sanitation steps were completed.
As with all new processes deployed and tested in a live working environment, gaps were inevitably discovered. But, in this case, any procedural or process gaps were sensed and could be actioned in real time!
Using Acadia, employees could quickly and easily identify process gaps and feed them with context to managers while continuing to perform their work. The result was more immediate improvement in compliance, productivity and responsiveness. Managers were in a position to review gap feedback and make real-time adjustments rather than waiting until the end of the shift and risking more potential accidents or gaps.
Acadia also allowed managers to revise work instructions in real-time and put them into the hands of the very next employee to perform the task. The ability to make quick adjustments applied to both office and plant environments. Normally compliance is tracked via two different sets of systems; one for business office processes and another for plant operations. The use of one system for both enhances scale and compliance across the business as a whole.
In this particular company, use of Acadia helped create efficiencies and improve line yield in operations before the pandemic. The same system is now helping to provide critical new work instructions and compliance requirements to keep employees safe.
2. Sensing from the Edge
Ensuring that employees understand and follow One Best Way processes is the first foundational step in creating a safer and more compliant working environment.
The advent of the pandemic brought new infection testing and working safety requirements. For example, checking for individuals with high temperatures and maintaining social distancing in the workplace is a challenge for the business to continuously enforce due to constant updates in protocol and training. An additional challenge is that these new requirements tend to be spread across multiple departmental systems. Procedures need to be integrated in order to holistically drive behaviors. The business needs to track performance in real time to determine if someone is coming to work with a high temperature and whether or not workers are consistently maintaining six feet of separation.
Fortunately, we can look to new digital operating capabilities to address these challenges. Recently, the digital twin cloud solution from the software company Cloudleaf has been used to help businesses accurately sense the location and condition of individual products (temperature, humidity, vibration, etc.) as they flow through the supply chain. The increasing sophistication of digital sensors, beacons, and wearables has expanded visibility to asset performance, supply stock accessibility, product quality, workforce availability, and more.
As businesses continue to adjust to the post-COVID19 world, these enhanced digital capability solutions will be applied with greater frequency to employee-orientated safety situations. One national retail client of Cloudleaf is moving forward with this capability presently by adopting Cloudleaf’s Safe2Go solution. Expect to see employees using wearables that track temperature, blood pressure, and location, providing real-time visibility of personal health vitals for compliance and safety purposes. As these safety procedures and tracking capabilities develop, they will also help with social distancing and contact tracing.
Augmented analytics provide significant performance management analyses to the business as well. The device history can be tracked to identify employees who came in close proximity to someone who has recently tested positive for the virus.
Last month, a leading US auto manufacturer started a program to test wrist devices that will buzz when employees come within six feet of one another. This device works in concert with other devices such as infra-red sensing cameras placed at plant entrances to check employee temperatures. All this infrastructure and new holistic capabilities help minimize outbreaks and disruptions.
Beyond testing the deployment of new devices, this company has already made major changes to their line processes and has rechoreographed tasks that previously required two people to work inside the vehicle together.
Continuously updated One Best Way procedures, combined with new tools for end-to-end visibility of workforce safety, dramatically changes the health and safety environment. Businesses that utilize these capabilities are in position to safely bring their employees back to productive work.
3. Augmented Planning Insights
As compliance and performance management process and sensing tools evolve, they will generate significant quantities of valuable data. The data can then be used to improve both operations and employee safety.
It’s important to remember that masses of data have little value without the tools to create the right event trigger alerts and render them into actions for the business. This knowledge creation from data will become a critical performance management capability, and it will be increasingly underpinned and enabled by the sophistication of augmented analytics such as AI.
For many global enterprises, effectively managing the end-to-end supply chain is critical. Planning tools, such as the solution from the software company Bluecrux, ensure the right product is manufactured and shipped from the distribution system to meet demand. In leading manufacturing operations, tools are extending the reach of the enterprise and incorporating data from suppliers, trading partners, and customers. This makes end-to-end supply chain to the customer visible and controllable.
Now is the time to augment planning tools and processes with health and safety data.
Data from process systems can help identify locations that are not properly following safety protocols, presenting a potential disruption risk to the business. These insights, combined with sensor data on the overall health of team members in plants, can help a company identify potential problems and risks before operations are actually impacted. This capability to predictively analyze operations will allow a company to shift capacity between locations, or move to another country, or even move to an unaffected business partner. The key capability is real time status and visibility!
In the future expect to see dynamic businesses that are able to sense changes before they occur. They will continuously maintain and track employee safety while simultaneously responding to fluctuating spikes in demand.
Start Today
With these new tools and capabilities in place, employees can feel safe returning to work. Companies can feel more confident in their ongoing ability to meet demand safely with employee health and safety in mind. In addition, customers can be assured that the products and services they need will arrive without unplanned disruptions, risks to themselves, or risks to the people who produced them.
This is the new architecture of emerging tools and processes to help businesses bounce back from the current pandemic crisis. Consistent utilization of these capabilities will also help overcome inevitable future crises likely to be caused by health and safety issues, natural disasters, country conflicts, or changes in regulations.
If you haven’t yet addressed any of the three keys described, I challenge you to create an immediate action plan and roadmap to incorporate them into your own operations. Plan to extend and deploy these capabilities in a phased and controlled manner over time to support the performance and success of your entire global enterprise.
Your new business focus should be to increase business agility and resilience to changes and disruptions, whether planned or unplanned. The result? Your business and your people will be successful and safe.
About the Author
Bill Read is a senior advisor and board director with more than 35 years of global experience and accomplishments in business and philanthropy. He currently serves on SAI’s board of advisors. His deep industry expertise and extensive network across key product manufacturing and retail industries have helped his clients achieve proven, sustainable improvements in overall P&L performance and product speed-to-market. Prior to his retirement from Accenture in April 2016, Bill directed the management consulting component of Accenture’s $8 billion consumer, retail, and industrial products business.
Ready to crush your goals?
"*" indicates required fields