Shifting production capacity in response to the trade war
Nowadays it’s not enough for manufacturers to have facilities in other markets, the offshore locations need to operate efficiently too.
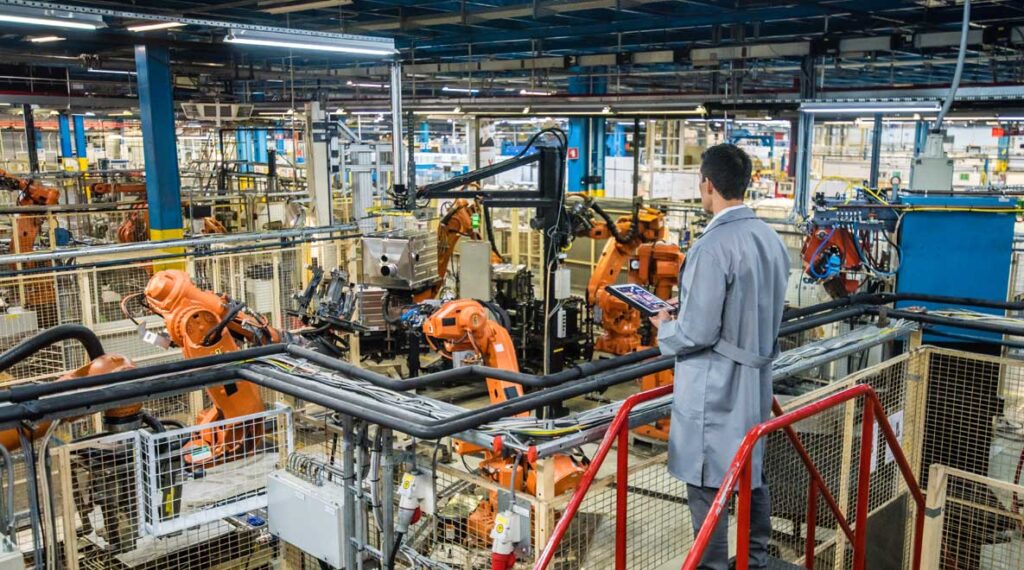
Early in 2018, the U.S. Department of Commerce launched a series of initiatives to eliminate the $700 billion a year trade deficit for non-petroleum goods, in an effort to increase US manufacturing jobs.1 Since then, the US has seen a wide array of counter-tariffs and threats of retaliation against US manufactured goods from whiskey to motorcycles.
Uncertainty as to what might come next from Washington or retaliating foreign governments makes it difficult for manufacturers to effectively plan the production processes necessary to serve various markets with competitive pricing.
If nationalism and reciprocity continue to replace global trade practices, the inevitable outcome for some manufacturers will be to move production to where they will sell their product.2
Harley-Davidson was one of the first companies to respond in this way. When the EU increased its tariff on motorcycles from 6% to 31%, Harley-Davidson claimed the tariffs would reduce its profits by up to $100 million annually and announced it would open new production facilities in Europe.3
There has been quite a bit of speculation that Harley-Davidson was already planning a move to Europe and that allowed them to make this decision so quickly after the new tariffs were announced.
Companies that have a presence in other territories and those operating flexible manufacturing systems (FMSs) will have a substantial advantage in this volatile environment. The one thing that is frequently overlooked, or at least not optimized, is the process of standardizing production in different regions through the deployment of consistent cross-geography manufacturing processes.
Alternatives already in pursuit
One of the biggest targets of the U.S. trade war is the trade imbalance between the US and China. For decades, companies from all over the world have been moving production to China to take advantage of lower cost labor, government subsidies and lax regulation. Even as early as the mid-80s these incentives were attracting companies like AT&T, United Technologies and General Motors from the U.S.4
In recent years, labor costs in China have been gradually increasing along with the size of its middle-class. Other incentives have started to dry up and increased risk to intellectual property has driven some companies to reshore manufacturing back to the US or to alternative low cost labor markets in Vietnam or Mexico. 5
The recent trade developments have accelerated these trends and created uncertainty for manufacturing company leadership teams as various regions are singled out, quickly reducing production planning options.
What’s clear is that manufacturers already operating in multiple locations around the world, are more flexible and can adapt faster to changing tariff conditions. Others may lose out.
Winners and Losers
In this environment, companies that are the most flexible will come out on top. Manufacturers with a global footprint, that can shift production capacity across borders will operate with an advantage. But moving production capacity isn’t enough. They will also need to limit downtime and decrease production costs without diminishing quality.
In 2016, reshoring accounted for a net positive 30K jobs in the U.S.6 This happened after the recession when companies were forced to cut costs and learn to be more efficient. This is also about the time that new developments in inventory management and lean manufacturing practices started to become more common place.
By the beginning of 2018, these efficiencies were already making American manufacturers more competitive with world-regions that have cheaper labor. So now that tariffs are beginning to play a bigger role, simply moving production to a cheaper region may not be enough to make a difference.
Improving Efficiency Across Borders
Winning manufacturers in this rapidly changing market environment are benefitting from standardizing processes across regions, making every employee more productive and facilitating the ability to shift production across regions.
Companies using the Acadia Performance Platform are able to do this by transferring their One Best Way processes seamlessly to other production facilities. This helps them quickly and inexpensively accelerate performance for both managers and team members regardless of where in the world they’re operating.
Acadia begins with a search driven knowledge repository that helps team members quickly find the right job aid when they need it, in any language
As information is shared with employees, Acadia provides an easy and intuitive way to track content consumption and compliance across the entire workforce.
Using quizzing and in-person evaluations gives managers a fast, accurate and inexpensive way to measure knowledge comprehension and identify who needs more training.
The platform also provides several ways to optimize processes incrementally as employees perform their work. Standardized procedures are easily converted to checklists that can be carried out to the shop floor on any mobile device working online or offline. Employees also have an easy way to provide feedback on individual tasks when process improvements are identified.
Gaining production flexibility has been a key objective of manufacturers for the last 50 years. Getting there quickly and inexpensively while avoiding negative customer impact is a recent development with an increasingly short runway.
As always, we would love to hear about how your organization is dealing with the need to shift capacity and other manufacturing challenges. Please drop me a note at tsmith@systemsalliance.com if you have questions or would like to discuss any of this further.
Sources:
- Reshoring Is on the Rise: What It Means for the Trade Debate
- Carmakers warn of production shift to avoid tariffs
- Harley-Davidson warns European tariffs will cause a ‘tremendous cost increase’ (HOG)
- Manufacturing Offshore Is Bad Business
- The 3 Countries Stealing China’s Business
- Why U.S. Manufacturers Are Turning Their Attention to ‘Reshoring’
Ready to crush your goals?
"*" indicates required fields