Downtime Improvement Yields $500k Savings in First Year
Downtime in manufacturing means dollars lost. The longer and more frequent the downtime, the less product is shipped, and the more resources are lost to waste. For some critical processes, improving downtime, planned or unplanned, can mean millions of dollars saved across the enterprise.
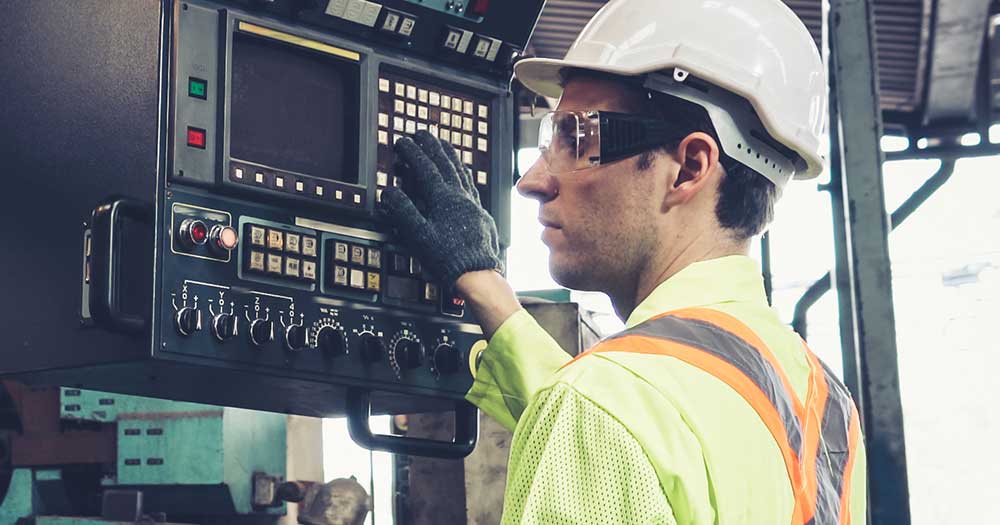
Downtime Improvement Outcomes
- $500k cash savings due to process change that led to decrease in error rate, rework, and planned downtime at a single facility
- Reduced time to proficiency for new hires and existing employees
- Higher retention rate of new skills among those trained using the new method
“It’s amazing how quickly we saw a difference in performance. To hit 19% improvement in just two weeks was unimaginable.“
– Continuous Improvement Lead
New Capabilities
- Repeatable, scalable training process that rapidly improves results
- Consistent execution of planned downtime procedure
- Training outcomes reinforced in workflow
- Identified opportunities to improve process
- Identified team members who need more training support
Our client is a consumer durable manufacturer with plants operating around the globe. A common procedure requires planned downtime 20-30 times per day at each of their facilities. At one of their largest facilities, it happens up to 60 times per day. Operations leaders understand that shaving even a few minutes off of that downtime can generate significant savings—but achieving meaningful downtime improvement was challenging. With a complex process and frequent operator turnover, the team needed a better way to ensure the process was executed accurately each time.
Continuous improvement managers at one plant replaced traditional shoulder-to-shoulder training with a more consistent and repeatable process in Acadia. Each team member was required to read and acknowledge the proper preparation and execution of the procedure. Then, they were quizzed on the information. Finally, they were observed and formally evaluated executing the procedure live. All of this information was tracked in Acadia to identify team members who needed additional support and aspects of the process that needed reform.
So what’s 8 minutes worth? The team saves $500,000 by bringing their procedure time down from 15 minutes to 7. After just two weeks of training using the new method, the team had already improved their planned downtime by 19% and reduced product waste. When implemented across all plants producing the same products, the savings will be in the millions.
Ready to crush your goals?
"*" indicates required fields