Fast moving beverage companies can’t afford to wait for paper
Improve line yield and eliminate waste by making your front-line operators more efficient.
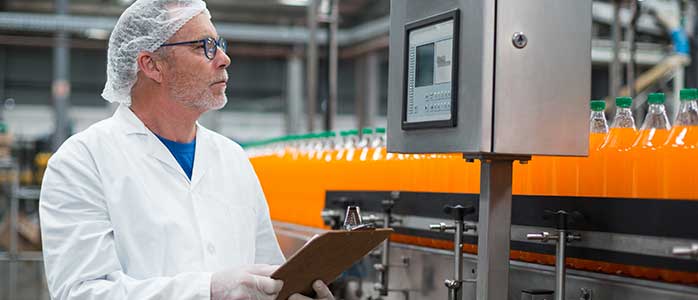
Imagine if each of your teams could:
- Cut waste from packaging and product changeovers
- Reduce low fills and non fills that impact yields
- Eliminate unplanned downtime and improve maintenance results
All of this is possible when you stop using paper and network drives to deliver work instructions and job aids to your teams on the line.
Human error is responsible for 23% of unplanned downtime in manufacturing
It’s impossible to eliminate all mistakes from our workflow. What we can improve is SOP compliance – eliminating repeat mistakes that cause injuries, waste, and inefficiency.
Provide your teams with the information they need to do their work correctly and they’ll make fewer mistakes. They’ll spend less time figuring out how to do things the right way. Instead, they’ll start offering suggestions for improvement.
Equip your team members with:
- Actionable, auditable work instructions and job aids
- Hands on micro-learning for new processes
- Feedback that helps them improve and advance
Make your process frictionless and your team will make changes to improve operations, spread best practices, and become more efficient. We can help.
When you integrate your team’s activity on Acadia with your production data sources. You’ll quickly see how SOP compliance for critical processes relates directly to your waste and productivity KPIs.
Is the bottle half-full or half-empty? Doesn’t matter, it’s going in the dumpster
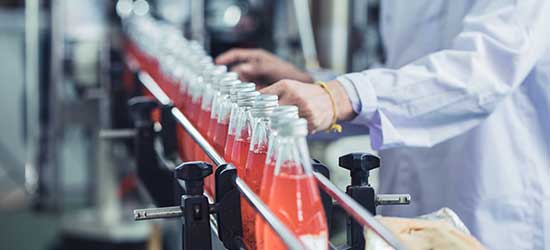
Changing sizes or products on a line can require multiple people from mechanics to operators and lab technicians. So, there’s lots of room for error between clean outs, sizing product feed and output, and calibrating package weights.
Acadia helps you activate corrective measures immediately when problems occur. With Acadia, each team member working on procedures like line changeovers will have precise instructions and job aids for their role in the process.
Managers will have insight into what stage of the process the team is in, who completed which steps, whether protocol was followed and how long it took.
Mechanical problems can lead to underfills, overfills, and empties

Downtime depends on the productivity of your maintenance team. With mechanics and other specialists in short supply, some Acadia customers are incorporating minor maintenance tasks into operator workflow. Things like regular lubrication can be added into SOPs for those already working the lines where it’s needed.
Deploying auditable SOPs to frontline operators helps ensure the critical tasks are done right and on time.
For more complicated maintenance procedures, Acadia SOPs can include diagrams, images, and videos that help your technicians complete them quickly and accurately.
Well-trained team members are more confident and stick around
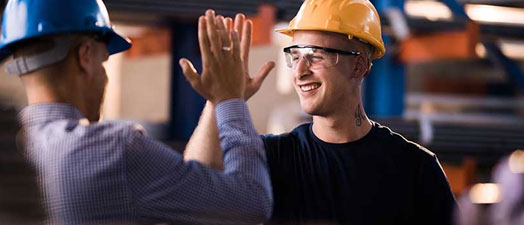
Everyone is struggling to find skilled workers for specialized roles and most are having trouble hiring even entry-level positions. Retention and upskilling have become an urgent priority for most companies.
The Acadia-enabled training process at a major beverage manufacturer works like this:
- The process begins on the plant floor – following One Best Way work instructions in the form of a task list, on a mobile device
- Quizzing and evaluations identify those who need more training support while allowing others to continue without interruption
- Engage employees by capturing process improvement feedback as part of task completion
Confidence is a major factor in employee engagement and retention. Bolster confidence by making knowledge tools and work instructions easily available.
You’ll hire and onboard faster, make teams more productive, and keep the people you have.
How can we help?
With Acadia, you can easily and inexpensively manage standard policies and procedures, track compliance, accelerate learning, and achieve behavior change.
Ready to crush your goals?
"*" indicates required fields