Getting to Zero Defect
The potential for perfection in manufacturing depends on your employees
- Quality issues can cost 10% or more of sales.1
- The total value of all product recalls last year was between $12.9 billion and $24.6 billion.2
- Quality incidents are more likely to happen when employees aren’t following proper procedures.
- Continuing with old tools, like paper checklists and binders, will only return poor results.
- A combination of technology, training, and focus can help make zero defects possible.
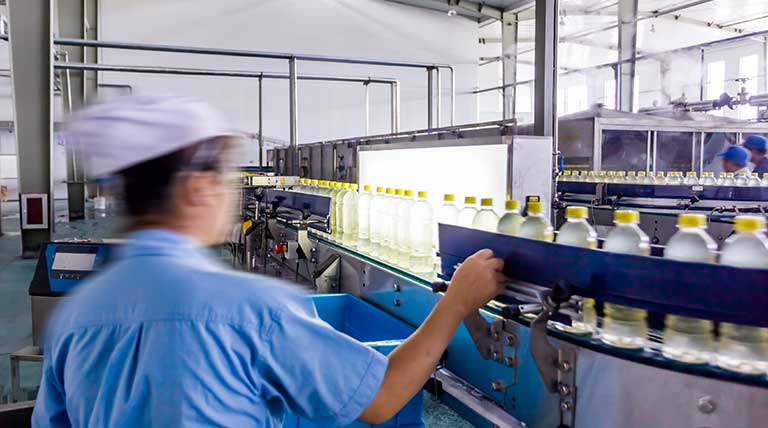
3.7 million pounds of food was recalled in a single incident when a supplier for a food manufacturer included milk in their breadcrumbs.3 Despite having great policies in place, the supplier’s employee(s) didn’t follow them.
The mistake was discovered after the breadcrumbs were already incorporated into batches of canned pasta, meatballs, tomato sauce, and chicken patties. Milk is a top food allergen and the products had been sold to U.S. schools and supermarkets. So, the manufacturer made the recall voluntarily out of an abundance of caution.
The average cost of a recall is in the millions, even small recalls that are caught early on can add up to 10% or more of sales.1 Last year, the total value of all product recalls was between $12.9 billion and $24.6 billion.2 That doesn’t include the value of product waste generated by defects that are caught before products ship.
Beyond the hard cost associated with recalls, manufacturers also suffer significant losses in reputation and potential future business.
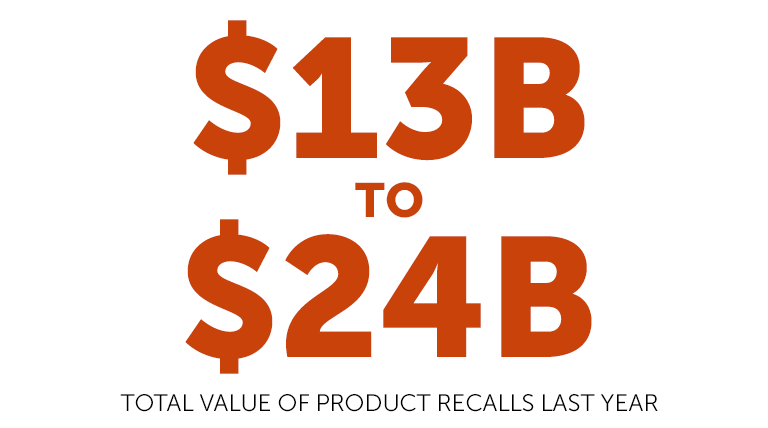
Most quality issues boil down to human error. And a majority of those events happen when employees don’t follow procedures – or don’t know what they are. In some cases, employees are trying to cut corners or feel pressured to speed up their work. In other cases, they simply received inadequate training.4
Amidst stubbornly persistent challenges, manufacturers are looking to an old approach for a solution. In pursuit of perfection, they’re bringing back Zero Defect Manufacturing – an approach that combines technology, training, and focus to eliminate defects.
But many producers are still arming their employees with old tools, like paper work instructions and shoulder-to-shoulder training. Despite whatever advancements they’ve made in automation in the last 10 years, those companies will continue to struggle with poor results.
Aiming at Zero Defect
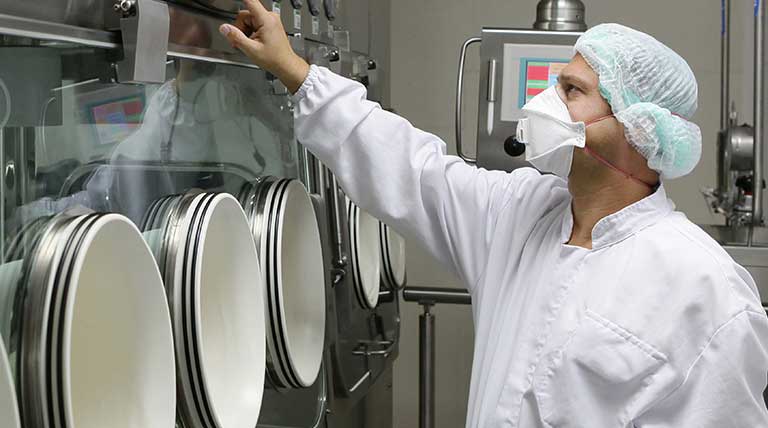
The Zero Defect concept gained traction in the 2010s as digitalization and Industry 4.0 initiatives were gaining ground.5 It focuses on rigorous quality control measures and preventing mistakes rather than repairing them. Many were hopeful they could automate their way around human error.
A decade later, manufacturers are realizing automation alone isn’t as perfect as they’d hoped. Outsiders tend to view the industry in an oversimplified way. They see it as a collection of processes and supply chains to be optimized, but it’s significantly impacted by the human-in-the-loop.5
Today, the Zero Defect approach emphasizes thorough inspections, strict adherence to procedures, and a strong focus on training and skill development to minimize human error.
Adding the Right Technology
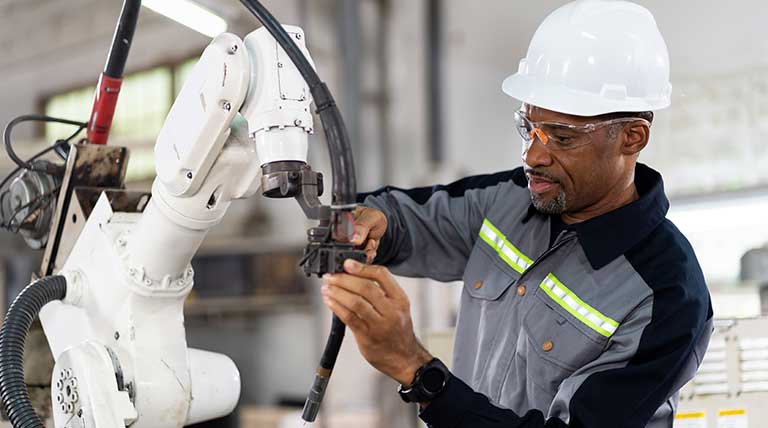
Technologies like collaborative robots offer an opportunity to augment employees, if they know how to use them. When people are a major consideration in the equation, transformation projects can be quickly adopted.5
Mistakes are made, machines go down, and the unexpected happens. You want your employees to be ready to respond as quickly as possible. Replacing binders with digital work instructions makes relevant information instantly available to your front line teams.
One of our clients hit unexpected downtime when a robotic lift failed. The engineer who originally installed the machine had recently left to go to another location. And no one else had been trained to troubleshoot it.
Our client could have wasted time trying to find a manual stuffed in a drawer somewhere or trying to repair it without one. But thankfully, before he left, the engineer created a trouble-shooting guide in Acadia. This enabled the contributors on the floor to quickly find an answer to their problem – saving hours of downtime.
Improving Training and Knowledge Accessibility
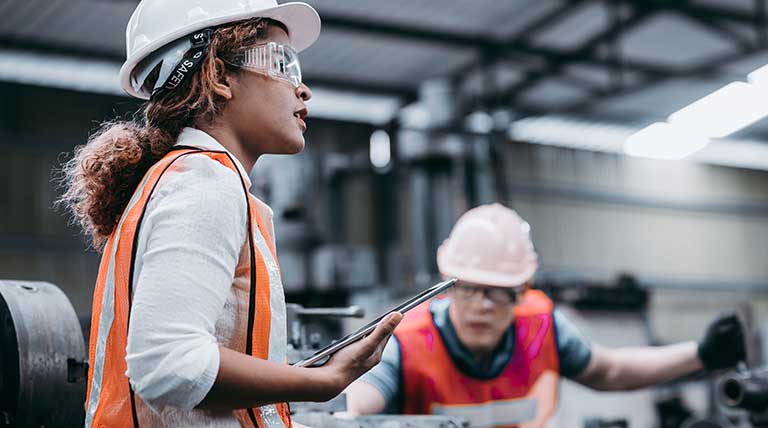
Certain tasks, like assembly operations, are becoming more automated. But automation isn’t replacing employees. It’s requiring new skills to do higher level work.
The average manufacturer can anticipate 800 hours of planned equipment downtime per year. Some of that nonproductive time can be recovered when in-house technicians are trained to complete maintenance activities efficiently.6
In the 1960s, manufacturers used posters to encourage employees to do their jobs right the first time.1 You can offer them a bit more.
Digitalization has made it much easier to put work instructions and visual job aids in the hands of your employees while they’re working. This capability makes it much easier to build, track, and mobilize your team’s skills to improve your business.
You can upskill employees on the floor to fill gaps in your workforce by equipping them with tools that enable them to learn on the job. You can track the capabilities of each team member based on their adherence to work instructions. And your employees will rely less on their colleagues as they learn.
When one of our clients experienced a wave of retirements, they realized their training program was not designed for a large influx of new people. They needed to build and track the skills of new technicians who were just beginning their careers.
Because the company hadn’t previously experienced much turnover, their training consisted of splitting time between reviewing manuals in the facility’s library and shadowing technicians on the floor:
- The library was entirely paper based
- Employees had to leave the floor to search for information
- They had to wait until a machine broke down to shadow an employee who could fix it
None of this met their sense of urgency to replace retiring team members.
They turned to Acadia to transform their paper-based system into a dynamic knowledge repository where the entire workforce can find the information they need, the moment they need it.
Now they have a structured onboarding path with step-by-step, on-the-job training for technicians that allows new hires to work autonomously. SOPs are delivered digitally with videos and other job aids they can access on the plant floor.
Acadia lets them set up training paths to teach team members the skills they need. And rather than waiting for a machine to break down to show a technician what to do, they can create procedures in Acadia that help guide new hires through the protocols instead. It’s allowed trainers to drastically reduce the time it takes to onboard technicians and make them intermediate users requiring no assistance.
Now, what used to take 500+ days only takes 125 with Acadia.
Building your employees’ skills improves quality and reduces costs from fewer mistakes, less rework, fewer delays, and better use of machines and materials.3
Crystallizing Focus on Process
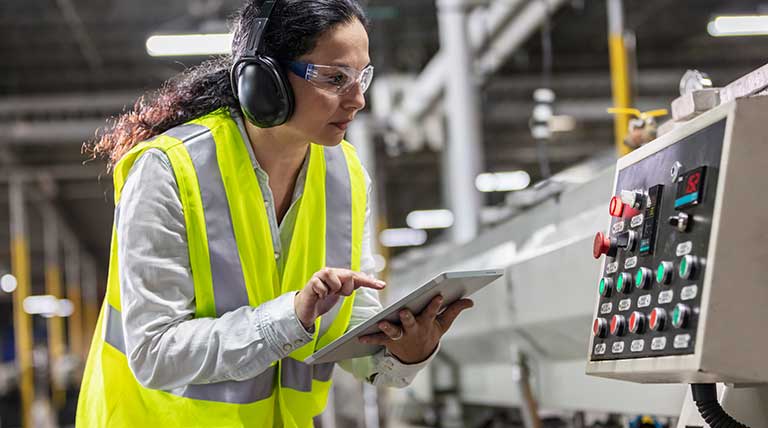
You’ll only get to zero defects if you have strong processes and your employees follow them.
A durable goods manufacturing client had a procedure requiring planned downtime 20-30 times a day. At one of their largest facilities, the procedure happens up to 60 times per day.
With frequent operator turnover and limited access to SOPs, they found that nearly every employee had their own way of completing the procedure. Inconsistency made downtime stretch to 15 minutes and beyond. They needed a better way to ensure the process was executed more efficiently each time.
They created SOPs in Acadia that each team member was required to read and acknowledge. Then, they were quizzed on the information. And finally, they were observed and formally evaluated executing the procedure live.
Acadia tracked all this information and made it easy for managers to identify team members who needed additional support as well as aspects of the process that needed reform.
After getting everyone working from the same playbook, the team reduced downtime from an average of 15 minutes to 7 in just two weeks! By the end of the year, the initiative had saved the company $500,000.
Invest in your most valuable resource
Zero defect manufacturing is possible. Your workforce has the potential to get you there. Give them the tools that make it easy to follow your standards and you’ll see improvements across the enterprise.
If you’re ready to build your employees’ capabilities, increase efficiency, and improve productivity, let’s talk.
Sources:
- American Manufacturers Seek Perfection as Quality Issues Mount
- New Report: Product recalls, warnings and penalties all increased in 2023
- Human error led to recall of 4 million pounds of food due to milk allergen
- 9 Maintenance Disasters: The heavy price of improper maintenance
- Advancing zero defect manufacturing: A state-of-the-art perspective and future research directions
- Understanding the Financial Cost of Downtime in Manufacturing
Ready to crush your goals?
"*" indicates required fields